Next generation IC heat spreader – Malico Tungsten Copper
Next generation IC heat spreader
-
Malico Tungsten Copper
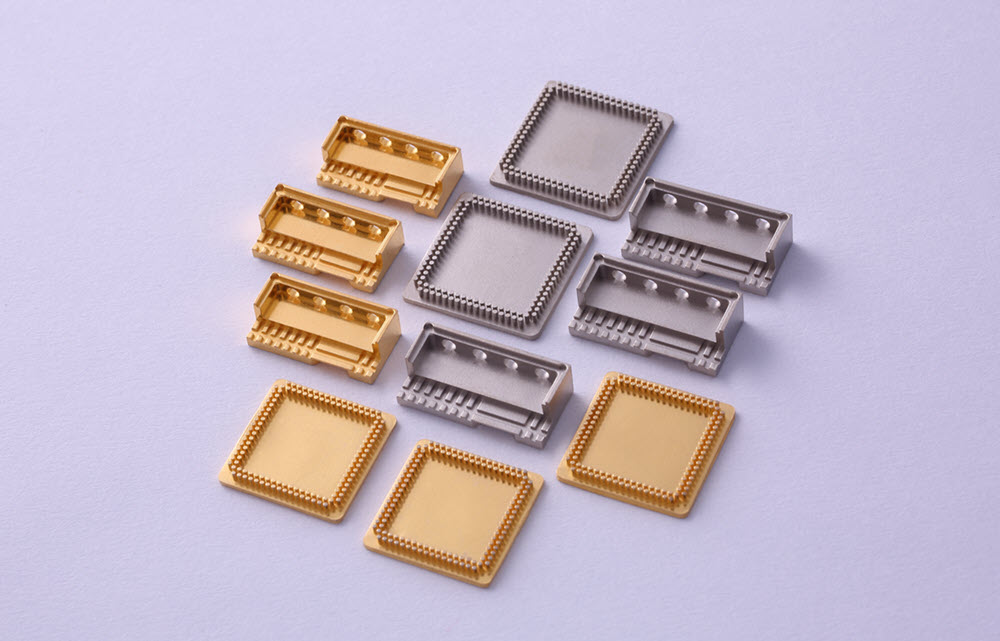
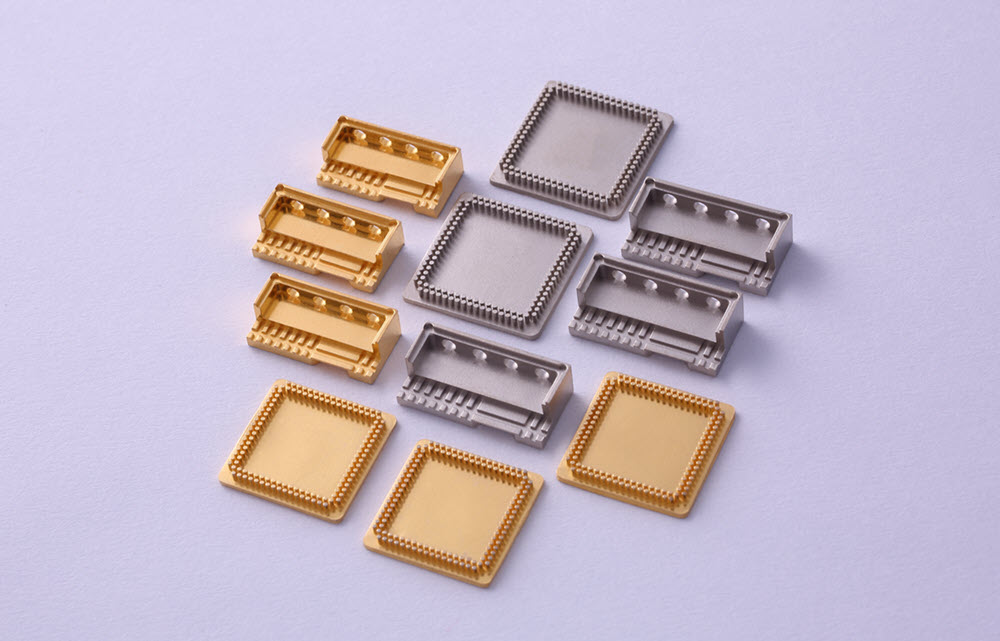
-- | thermal conductivity | coefficient of expansion | forming | cost |
![]() |
180~200 W/mk | Good matching 8.2 x 10-6/K |
good | competitive |
copper | 390~420 W/mk | Too high 16.6 x 10-6/K |
fair | competitive |
aluminum | 200~220 W/mk | Too high 25.0 x 10-6/K |
good | competitive |
silicon carbide | 340 W/mk | Good matching 4.0 x 10-6/K |
difficult | expensive |
-- | Footprint | Pin number | Surface area | Pitch |
![]() |
15x15mm | 400 pins | 808mm² | 0.75mm |
Stamping | 15x15mm | 0 | 225mm² | 0 |